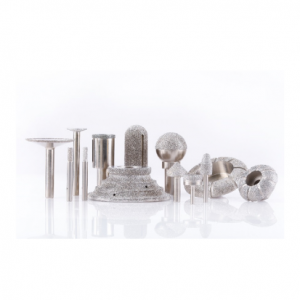
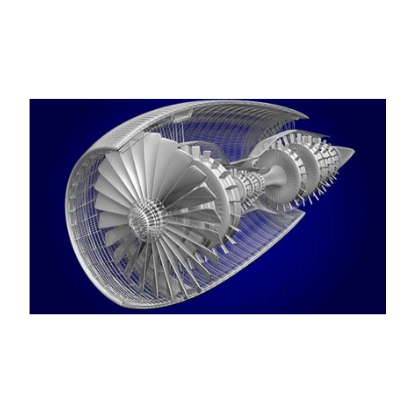
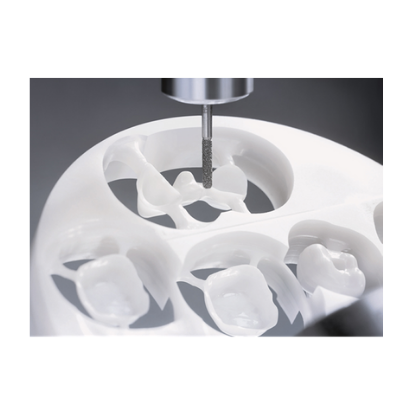
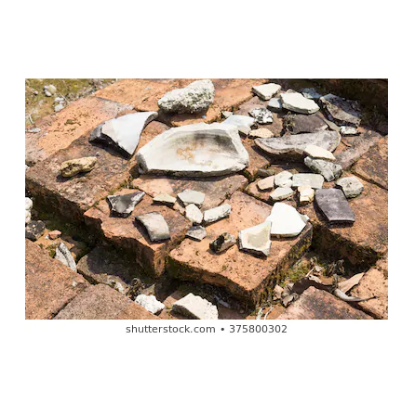
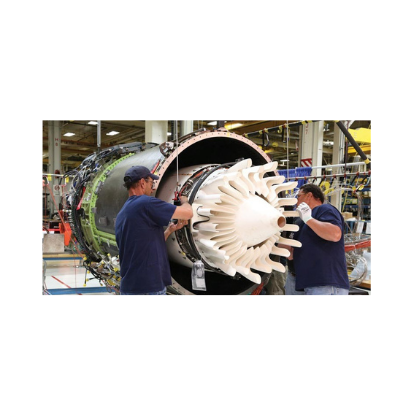
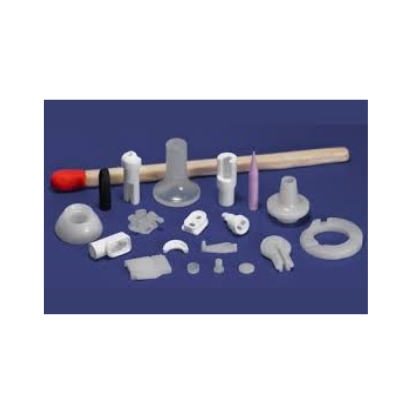
Solutions for
Ceramics and CMC
The word “ceramic” is derived from the Greek word κεραμικός (keramikos) meaning pottery.
Ceramic material is an inorganic, non-metallic, often crystalline oxide, nitride or carbide material. Some elements, such as carbon or silicon, may be considered ceramics. Ceramics are heat resistant, they can be used for many tasks for which materials like metal and polymers are unsuitable. Ceramic materials are brittle, hard, strong in compression, and weak in shearing and tension.
Ceramic materials are used in a wide range of industries, including Aerospace (Engines, Airframes, Space shuttle, Unmanned Air Vehicles) Medicine & Dental, refinery, Mining, Electronics industrial, transmission electricity.
In aerospace applications, ceramics are primarily found in engine and exhaust systems, thermal protection shields, and structures for ultra-high-speed flying objects. Ceramics and ceramic matrix composites that can withstand temperatures as high as 1,600°C are used to manufacture lightweight turbine components that require less cooling air, such as vanes, blades, nozzles, and combustion liners, and parts for the exhaust system that enhance acoustic attenuation and have a long life thanks to their abrasion and corrosion resistance.
Ceramic-matrix composites (CMCs) comprise a ceramic matrix reinforced by a refractory fiber, such as silicon carbide (SiC) fiber. CMCs offer low density, high hardness and superior thermal and chemical resistance. CMC components have greater durability and heat resistance. CMCs is highly attractive in a vast array of applications, most notably internal engine components, exhaust systems and other “hot-zone” structures, where CMCs are envisioned as lightweight replacements for metallic superalloys. The demand for CMCs is expected to increase over the next decade, according to jet engine and aircraft systems manufacturer. SiC CMCs can withstand temperatures greater than 2400°F/1316°C. This and their reduced weight (one-third the weight of nickel superalloys) make them attractive to engine manufacturers that are looking for weight reduction in the engine hot zones in pursuit of greater fuel efficiency.
Machining Ceramics is a professionally demanding task, ” M.D.T INDUSTRY ” Diamond Electroplating process is the most recommending solutions for Grinding & Drilling Ceramic & Ceramic-matrix composites (CMCs).
DIAMOND ABRASIVE GRITS TOOLS STARTING FROM 0.4 MM / 0.0157″
Part of Schneider Group, MDT Industrial is a worldwide manufacturer of diamond/CBN abrasive grits tools.
Since 1990, MDT Industrial specializes in design and manufacture of precision diamond abrasive grits tools for grinding, cutting, deburring, drilling, trimming and polishing of abrasive materials such as: Composites, Honeycomb Composites, Graphite & Kevlar, Reinforced Plastics, Ceramics, Fiberglass, High Temperature Alloys, Tungsten Carbide, Inconel and more.